CELLUWOOD
Wood-like BioComposites
CelluWood is a clade of chitosan-cellulose composite materials, combining various circular cellulose fillers and biomimetic adhesive-polymer formulations inspired by the adhesive structures of mollusks. By using the molecular building blocks of life and using biomimetic chemistry to make it biocompatible, CelluWood degrades into a biostimulating fertilizer at its end-of-life with out compromising mechanical performance during its intended use.
It is emision free, formaldehyde free, carcinogen free, and produces no toxic byproducts*, contributing to safer working conditions than treated lumber products (mdf, multiplex, osb) and prototyping foams.
It is designed for a suite of use cases; ranging from compostable prototyping, reforestation products and indoor consumer products, to out-door, water-resistant formulations for use in furniture, semi-structural, to experimental structural formulations for application in the built environment.
Top left: Bleached Jute, top right: Jute
Bottom left: 150um pine flour, bottom right: coconut
From form to fertilizer
Biomimetic Chemistry
3 months after deposited in gravel-rich soils (left)
Initial Sprouting
6 months after deposited in gravel-rich soils (center)
Healthy growth
8 months after deposited in gravel-rich soils (right)
Luscious growth
Material: Lignin modified PROTO_CELL
FORMULATION
PROTO_CELL
+
Biomass
PROTOWOOD
-
PROTO_CELL is composed of high molecular weight Chitosan, Nanocellulose, and other cellulose starches.
With prolonged water exposure, the embeded biobased solvants begin to break down the bonds between the chitosan and cellulose products, separating the Chitosan and Cellulose biopolymers from one another. What is left is a weakly acidic slurry that can be used in compost and provide biostimulating properties to gardens with proper use. -
Compostable
Anti-microbial
Fire resistant. -
Compostable Prototyping.
Form Finding.
Temporary use products.
CELLUWOOD
BIO_CELL FLEX
+
Biomass
BIO_CELL FIRM
+
Biomass
-
BIO_CELL FLEX is a biopolymer adhesive composed of high molecular weight chitosan, nanocellulose, and other cellulose starches. Where traditionally, these materials are all water soluble, they have been ionically modified to be water resistant, while using the water molecule as a componant to elicit elasticity and flexibility.
In comparison, BIO_CELL FIRM is a non-brittle, non-elastic variation of FLEX that does not encorporate the water molecule into its structure. Similarly, it is a biopolymer adhesive composed of high molecular weight chitosan, nanocellulose, cellulose starches, but includes tannic acid to achieve its material properties.
BIO_CELL FLEX
pH 3.5 - 5.0
BIO_CELL FIRM
pH 3.0 - 5.0 -
Anti-Microbial
Fire Resistant
Water Insoluble -
Form Finding.
Injection Molded Products.
Molded Products & Furniture.
Experimental Architecture (non-load bearing).
FIBR_CELL*
+
Biomass
FIBR_CELL+
+
Biomass
-
FIBER_CELL, in both instances, is a combination of Chitosan (HMW), nanocellulose, cellulose starches, and tannic acid.
Designed specifically for experimental architecture, FIBR_CELL* is covalently crosslinked with glutaraldehyde - a safer albeit related chemical to formaldehyde. This allows FIBR_CELL to have similar mechanical properties as a urea-formaldehyde (UF) resin, with out using known carcinogens. While direct exposure to gluteraldehyde is known to cause irritation to mucus membranes, it is commonly used for crosslinking chitosan products used in biomedical applications within the human body, and considered 40 times safer than formaldehyde.
In dedication to producing fully Bio- materials, we have also produced a FIBR_CELL+, which is covalently crosslinked with Genipin, originating from Gardenia fruits. It is purly biological and considered much less toxic than gluteraldehyde - however the production of this crosslinker is not nearly on the industrial scale as -aldehyde chemicals. It is therefore is prohibitively costly for most applications, and reserved for projects where completly bio-materials outweighs material cost considerations. -
Anti-Microbial
Fire Resistant
Water Insoluble
Load Bearing (Experimental) -
Form Finding.
Product & Furniture.
Experimental Architecture.
FABRICATION
Liquid Disposition
Modeling (LDM)
LDM is optimal for minimal material from circular feedstocks. In combination with multi-axis milling and optimized part design, both complex geometries and high levels of detail can be achieved while taking advantage of the full binding power of the X_CELL adhesives.
In its LDM application, parts are oversized to compensate for shearing artifacts and shrinkage, assembled, and post processed using cellulose as its primary feedstock. Due to the adhesive characteristics, the mixtures of ProtoWood and/or CelluWood can be used to bind parts together during assembly, and post processed to remove seams - Illustrated with the stool prototype to the right.
Depending on the adhesive composition, which has been modified for rheological purposes, shrinkage varies from ~15-20%.
30mm/s
4-8mm
Wood Flour
150-500um
ProtoCell_modified
Assembly (glued with ProtoWood), Sanding, Yakisugi
Linseed, Beeswax
Print speed:
Nozzel Size:
Fiber:
Fiber Resolution:
Adhesive:
Post Processing:
Finish:
HYDROLIC PRESSING & MOLDING
In concert between traditional presses and 3D printed or milled aluminum molds, this methodology allows for an accurate fabrication method that also increases part strength, due to material compression.
Compared to LDM, the parts can be accurately modled. However burden then falls on molding expertise for complex mold design; where rudementary molds are appropriate for simple parts, blocks, and desings with low geomteric complexity, and higher order parts and products require much further consideration.
Adhesives in this application do not require additional modification, and shrinkage is much less substantial, ranging from ~8-10%.
Molding Material:
Nozzel Size:
Print Speeds:
Adhesive:
Pressing Force:
Post Processing:
PLA
0.4-0.6mm
250-400mm/s
ProtoCell
1-5 ton
Right (prototype) drilling and sanding
Left (optimized) minor flashing removal by knife
project inquiry
We are continuously looking for ambitious visions and design challenges.
If you're interested in collaborating, please leave your contact information and a brief explation of your project and we will get back you as soon as we can.
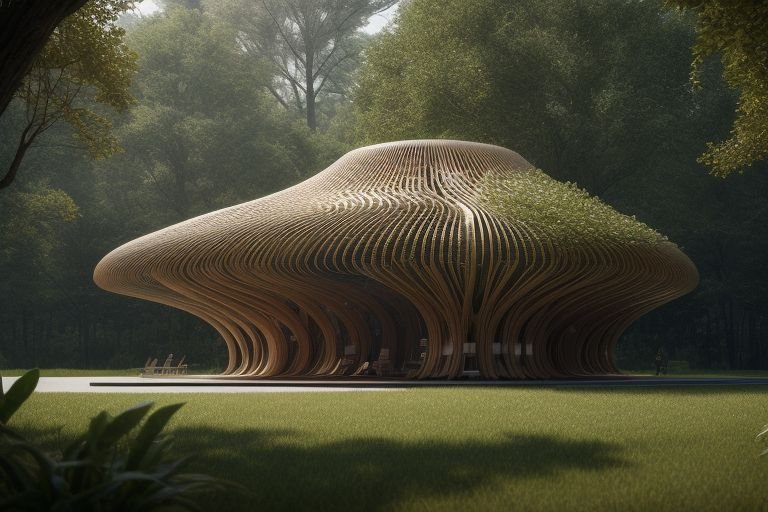
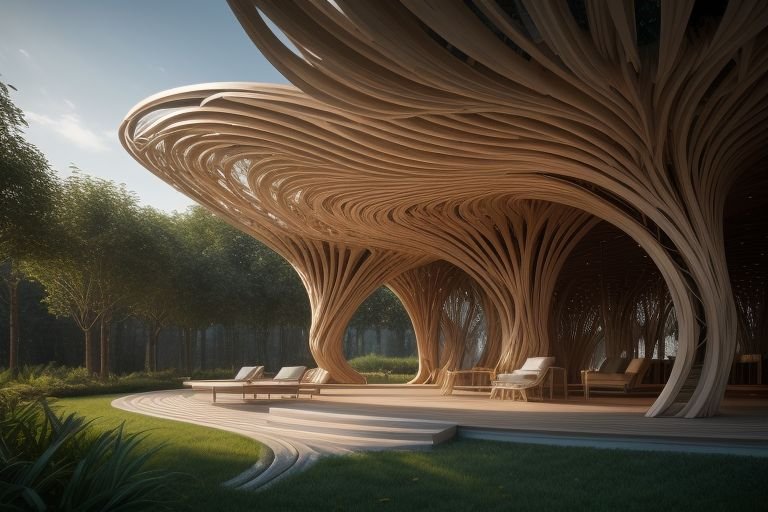






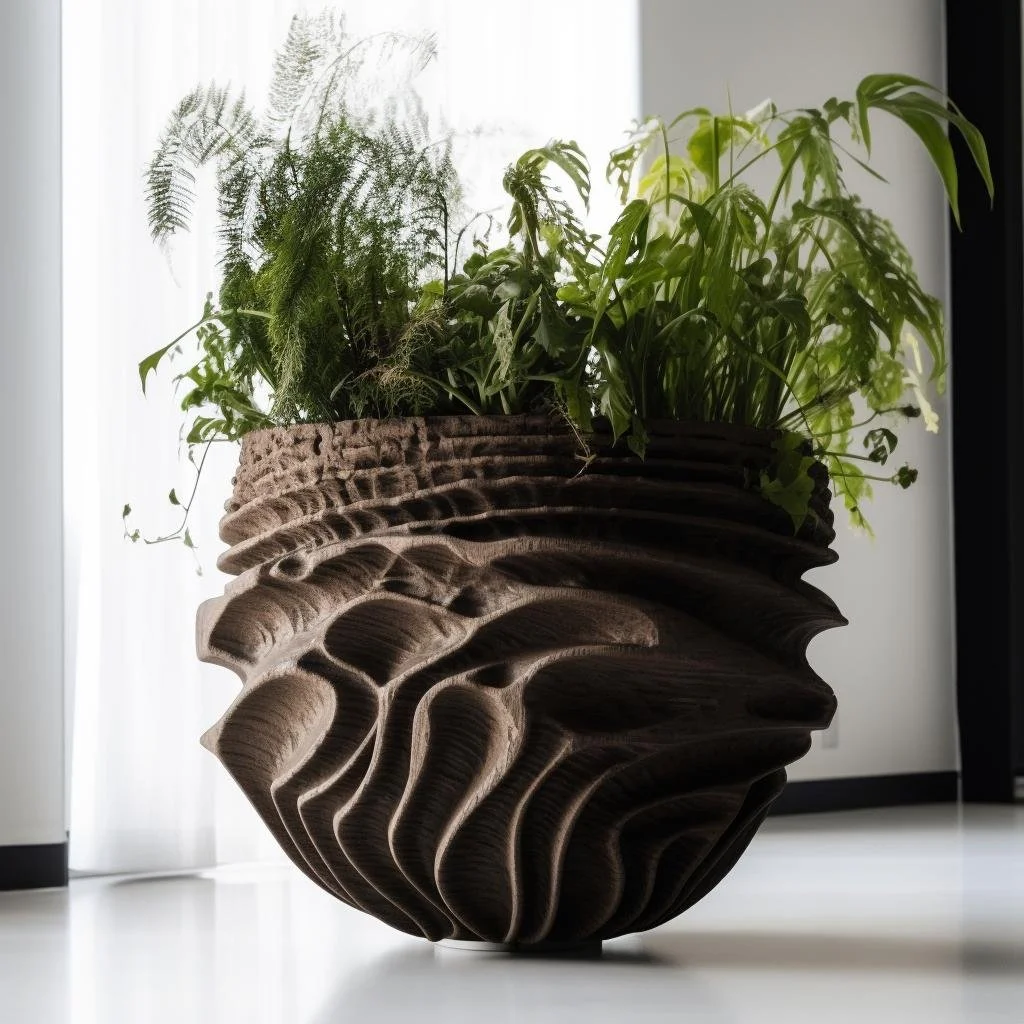
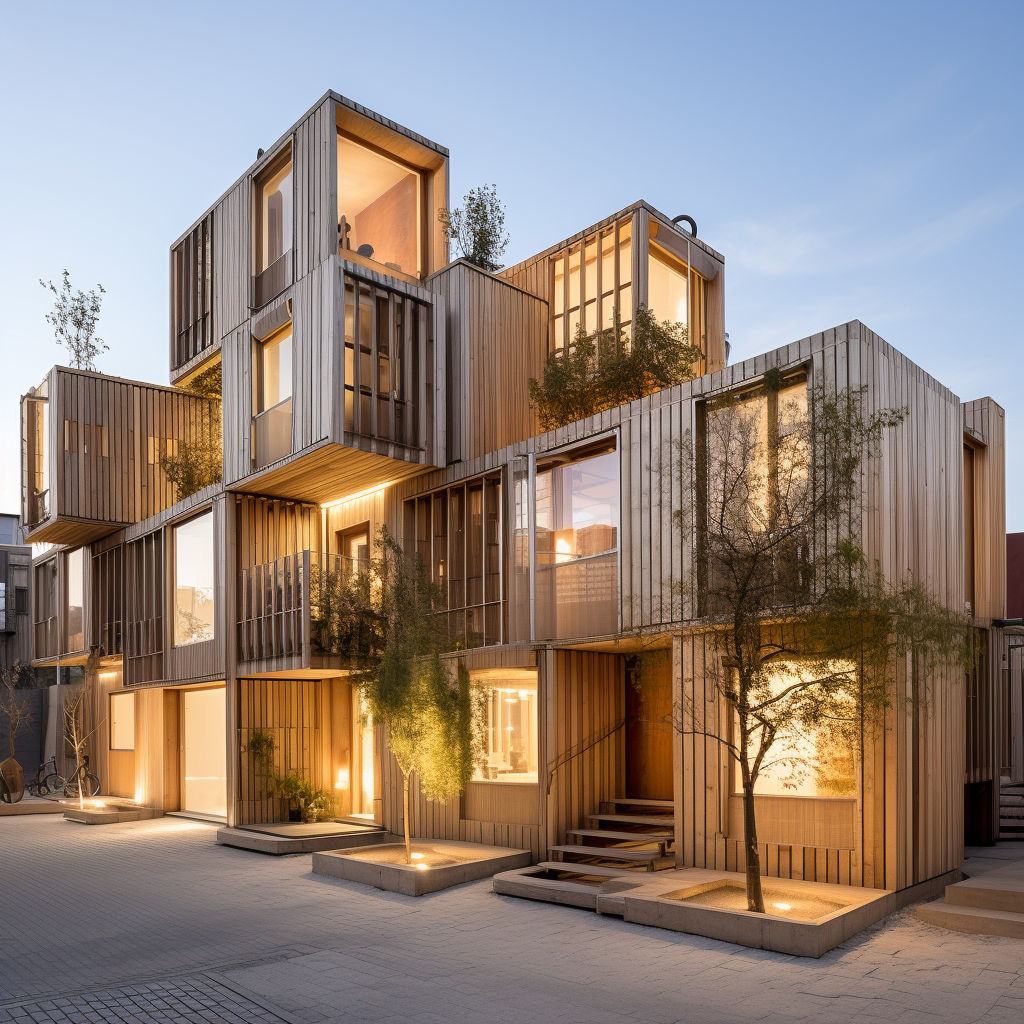
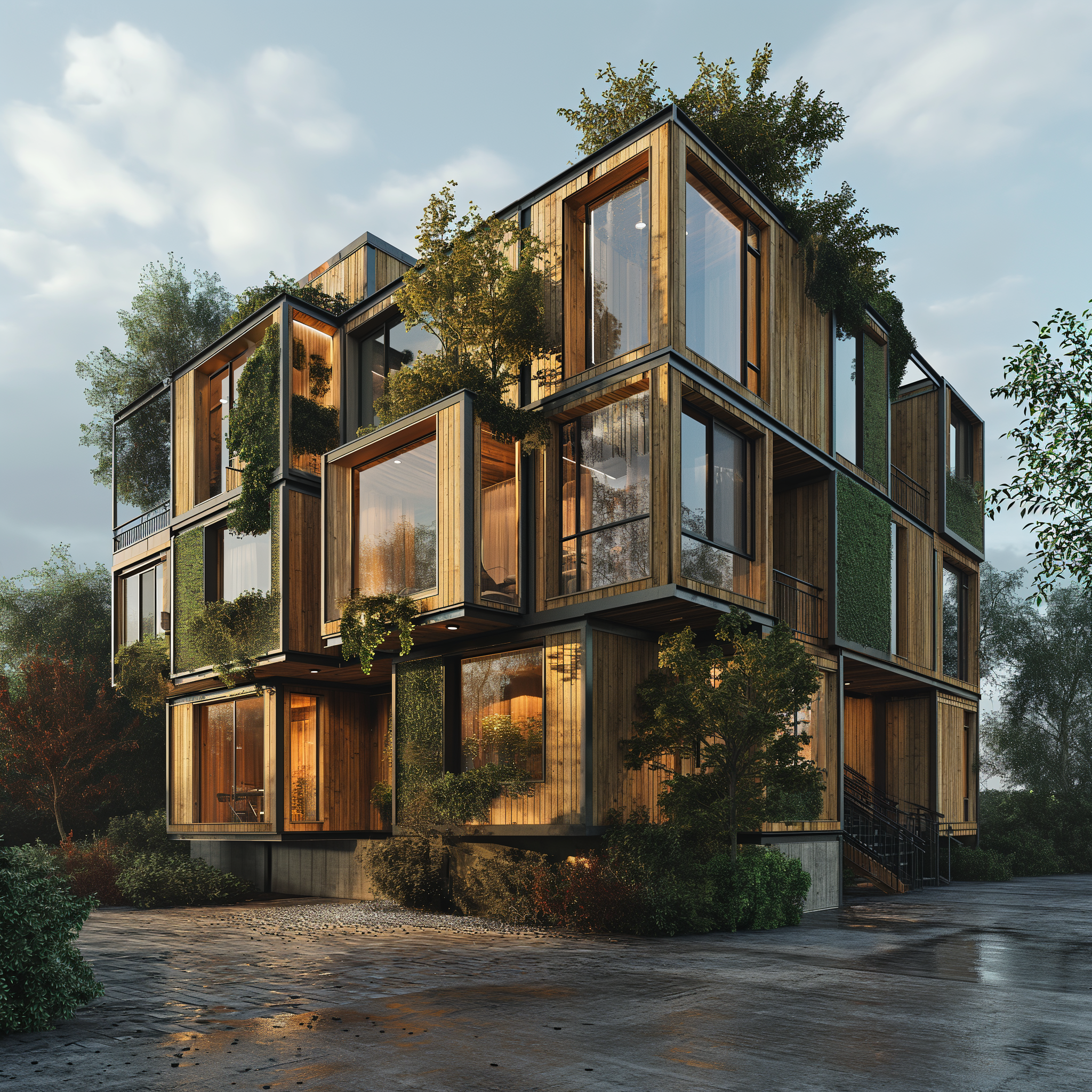
