
Sustainable Prototyping
Additive and Subtractive Manufacturing with Cellulose Composites
Prototyping Beginnings
My interest in Bioadhesives and Cellulosic Biocomposites started with a curiosity in sustainable rapid prototying materials. While working at MVRDV as their head of Digital Fabrication, I would spend a few days a week running an Open-Source CNC machine (OpenBuilds 1515), and would frequently check on milling projects through out the day; carfeully removing the mounted vacuum head and sucking away wood debris from site models that we would use to communicate large scale architectural projects. At a certain point, I looked at a few trashcans filled with milling waste and said to myself “I wonder if I could somehow convert that into a better prototyping material than bluefoam.”
For those unfamiliar with bluefoam, its the choice material for architectural models. Its increadibly easy to work with, requiring only a hotwire cutter and other basic tools, allowing architects to quickly ‘sketch’ ideas out in 3D. However, while it’s easy to work with, it also comes with a cost, both interms of health and sustainability. Bluefoam, or rather extruded polystyrene foam (XPS), is styrofoam, and when architects make models, they laser-cut it, sand it, and melt ths stuff in the process. While it may make for some gorgeous models, it also contributes to microplastic waste, produces toxic fumes while melting or heating, and is notorious for having an inability to biodegrade. Sanding the stuff generates fine particulate styrene plastics, which can easily become airborn, causing inhalation hazards and contributes to envionmental microplastic pollution - and simply using a hot wire cutter, which is the most common cutting tool for the material, produces styrene, benzene, toluene, carbon monoxide, and some instances hydrogen bromide gasses. Some of of these byproducts are classified as known human carcinogens, all of which are toxic to human health.
With a clear problem to solve, and an abundance of base ‘waste’ material, I started hitting materials science literature. Rather quickly into my technical dive into sustainable prototyping materials, I found a set of papers called “Sustainable Rapid Prototyping with fungus like adhesive materials, (FLAM)” and further “Large-scale additive manufacturing with bioinspired cellulosic materials,” both coming out of Singapore University of Technology and Design. They explored the use of the 2 most abundant polymers on the planet earth, Cellulose and Chitin in 3D printing, molding, and other subtractive manufacturing applications. For the applications in both additive and subtractive manufacturing, the SUTD team combined ratios of wood flour (really really fine saw dust) and nanocellulose (produced by grinding paper pulp into a fine paste), and then further deacytelated chitin, also known as chitosan, into various ratios until they found the right mixture of componants that was either printable (a rather viscous, pulpy substance), or hand moldable (relatively dry in comparison, like a slightly hard clay).
From my prior work exploration into nacre-like ceramics
Inspired by these works and through the network of MVRDV, I was introducd to 2 researchers from TU Delft looking into 3D printing with lignin and cellulose materials, later publishing “wood-based 3D printing: potential and limitation to 3D print building elements with cellulose & lignin,” who kindly provided an abundance of fibrilated nanocellulose and lignin for my own research. Further, sourcing chitosan from a large global distributor.
Left: prints from the publication wood-based 3D printing: potential and limitation to 3D print building elements with cellulose & lignin,
Right: prints and moulded parts from Sustainable Rapid Prototyping with fungus like adhesive materials
Following these introductions, I initially cast a series of 2.5cm^3 cubes, following the FLAM protocols of a 1:8 ratio of wood flour to chitin, however in this setting - I had not yet procured nanocellulose from the TU Delf researchers.
and diving deeper into composites and adhesives literature, I produced a small series of 3D printed columns for my undergraduate thesis entitled “towards living architecture.” From a technical perspective, this material explored and evaluated a combination of cellulose filler (wood flour; 150um, fibrilated nanocellulose) and chitinous (high molecular weight chitosan suspended in an alginate hydrogel) binders, as a redundant composite adheive technology.
The cellulose filler, inspired by the studies in FLAM and further “Strong and Tough cellulose nanofibrils composite films: mechanism of synergetic effect of hydrogen bonds and ionic interactions,” leveraged the comparative large particle size of wood flour, adding the hydrogen bonding potential
With support from:
Sustainable Prototyping
Additive and Subtractive Manufacturing with Cellulose Composites
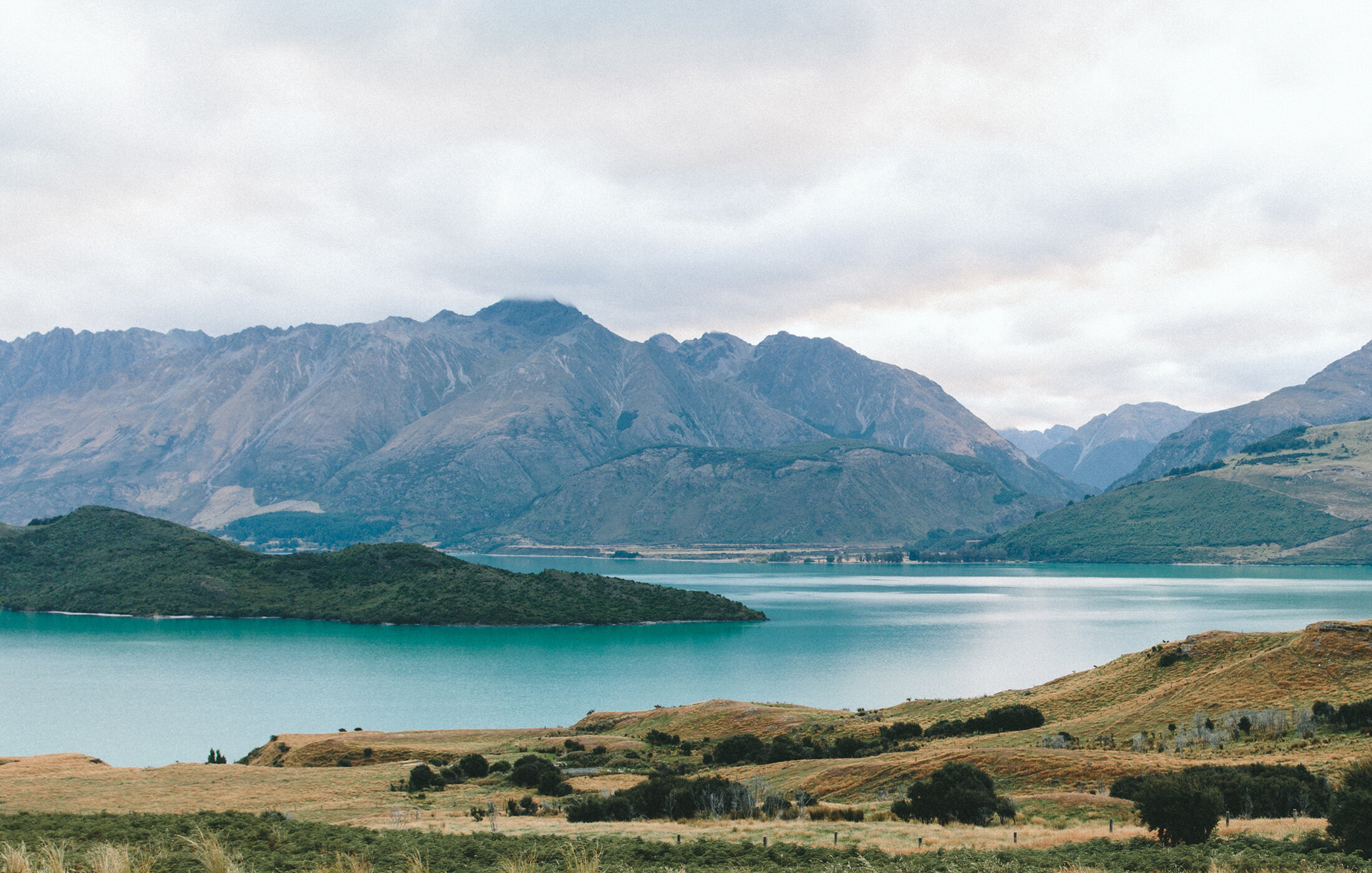